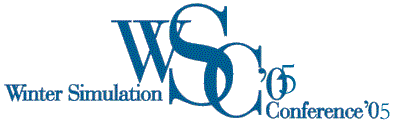 |
WSC 2005 Final Abstracts |
Manufacturing Applications Track
Monday 10:30:00 AM 12:00:00 PM
Assembly Systems
Chair: Edward
Williams (Production Modeling Corporation)
Analyzing Printed Circuit Board Assembly Lines Using
a Pcb Asembly Template
Pradip D. Jadhav and Jeffrey S. Smith
(Auburn University)
Abstract:
PCB assembly lines are characterized by asynchronous
transfer of parts resulting from variability in terms of random processing,
failure, repair, exhaust, and replenishment times. The throughput for such
manufacturing systems depends upon simultaneous availability of resources;
namely, machines, material, and operators. Further, random break-downs along
with the capacitated buffers cause blocking and starving which affects the
throughput. Analytical models for such system require simplifying assumptions,
hence simulation modeling is the popular choice. For simulation models to be
successful, capturing the impact of operator interference is important. This
paper describes a methodology developed for simulation modeling and analysis
of PCB manufacturing lines, capturing the complex interactions between its
components. A custom-developed PCB assembly template is used for modeling
purposes. Though the analysis described in this paper pertains to PCB assembly
lines, it is equally applicable to general class of serial production lines
with capacitated buffers.
Operator Paced Assembly Line
Simulation
Marvin S. Seppanen (Productive Systems)
Abstract:
This paper describes an Arena based operator paced
assembly line simulation model. Besides the normal flow of assembly units
between work cells, the model considers both the movement of operators between
cells and intermittent duties, such as equipment repair and material stocking.
Simulation results are presented for a 4-cell test case.
Intelligent Modeling and Simulation of Flexible
Assembly Systems
SK Ahad Ali (University of Toledo), Hamid
Seifoddini (University of WIsconsin Milwaukee) and Hong Sun (University of
Toledo)
Abstract:
A combination of product mix and production volume is
analyzed using a reconfigurable simulation model aiming to improve the
performance and optimal designing requirements. The performance under
different production scenarios is developed to find the optimal combination of
product mix to meet future customer demands. This research provides a
re-configurable assembly system modeling by adding flexibility and evaluates
alternative designs. The best satisfaction of the production requirements
under dynamic production is validated with real application.
Monday 1:30:00 PM 3:00:00 PM
High Volume Material Flow
Chair:
Guodong Shao (NIST)
Advanced Decision Logic in Simulation of Material
Flow Processing Networks
Douglas A. Bodner, Ke Wang, and Sheng Xu
(Georgia Institute of Technology)
Abstract:
Material flow processing networks are ubiquitous in
modern society. Such networks embody uncertainty, advanced decision logic, and
increased performance expectations. As such, they have been subject to
analysis by a variety of methods, with one of the most prominent being
discrete-event simulation. Simulation enables detailed flow modeling,
incorporates uncertainty and allows experiment-based performance assessment.
Traditional approaches to simulation are not well-suited to modeling advanced
decision logic, though. This paper explores the issue of representing advanced
decision logic and presents a reference model for material flow processing
networks to support such representations. Implementation issues are discussed,
as well.
High Performance Simulation in Quasi-Continuous
Manufacturing Plants
Lan Chen and Michael Pidd (Lancaster
University)
Abstract:
Though the quality of discrete simulation software
packages is high, most are aimed at systems in which discrete objects change
state as they move from work-station to work-station. This generic model is a
good fit for some manufacturing, for example, much automotive production.
However is not well suited to very high-speed quasi-continuous manufacturing
as found in the food and drinks industry. LanSkim is a prototype PC-based
package designed for these applications. It is simple to use and runs very
fast but is insufficiently detailed for all purposes. Adding full detail would
make the simulations run very slowly, hence we examine the use of parallel
computation to allow increased level of detail. We describe Lan-WARPED, based
on WARPED, in which is a parallel simulation models of such plant.
Fluid Based Simulation Model for High Volume DC
Conveyor Systems
Ying Wang and Chen Zhou (Georgia Institute of
Technology)
Abstract:
In this paper, we present a fluid simulation
methodology applying to high volume large conveyor networks operating in a
slowly changing environment, often found in large distribution centers.
Traditional discrete-event cell-based approach to simulate such networks
becomes computationally challenging due to large number of events resulting
from high WIP level, complex network and large conveyor footprint. The fluid
simulation model is built on a Petri-Net based framework. We present the model
and investigate the feasibility in modeling capability in terms of input and
release control logics, performance evaluation and computational savings.
Monday 3:30:00 PM 5:00:00 PM
Facilities Planning & Work Cell
Design
Chair: Kiran Mhajan (Hinz Nixdorf
Institute)
For Effective Facilities Planning: Layout
Optimization Then Simulation, or Vice Versa?
Esra E. Aleisa and Li
Lin (University at Buffalo)
Abstract:
It is widely accepted that simulation is an integral
part of any effective facilities planning or layout study. Traditional
approaches claim that layout optimization produces strategic results and
therefore should precede simulation analysis, which focuses on operational
issues. On the other hand, more recent studies suggest that running simulation
models prior to conducting layout optimization produces more realistic
layouts. In this paper, we contrast these two paradigms, with respect to the
general assumptions and the types of applications that advocates from each
paradigm have used to support their claim. In addition, we propose guidelines
on which approach to pursue according to the layout study objectives and the
characteristics of the system under consideration.
Validation of The Re-Design of a Manufacturing
Work Cell Using Simulation
Carrie Grimard (Robert Bosch
Corporation), Jon H. Marvel (Gettysburg College) and Charles R. Standridge
(Grand Valley State University)
Abstract:
Simulation can be used to validate the design or
redesign of any complex system before it is implemented. Validation evidence
is obtained if the simulation demonstrates that the system operation
corresponds to its design. This evidence includes comparing both detailed
system behavior and performance measure values to those stated in the design.
The application of simulation to validating the redesign of an injector
assembly and calibration production area is discussed. Simulation is necessary
to validate the initial estimate of cell throughput since a single worker must
perform multiple operations at multiple workstations. The feasibility of the
pattern of movement by this worker between stations must be demonstrated and
alternative patterns assessed. Controls on the amount of work in process
inventory in the cell must be validated. Modeling challenges unique to part
movement using one-piece flow, work in process inventory control, and the
movement of both workers and parts are discussed.
Applying Simulation to Interative Manufacturing
Cell Design
Sara L. Maas (Leon Plastics) and Charles R. Standridge
(Grand Valley State University)
Abstract:
Launching a manufacturing cell to be efficient and
lean, yet profitable, is a time-consuming process and is often based on many
assumptions. The utilization of simulation models to help design the cell and
the logistical structure to support it can expedite and streamline the
development process. Assumptions and designs can be validated to help insure
effective operations as soon as possible. We have developed a generic
simulation model and associated capacity analysis, schedule planning, and
target inventory setting software to support the computer based assessment of
the operation of cells typical to the plastic manufacturing industry before
capital investments are finalized. Model input describes a particular cell,
the products it produces, and customer demand for these products. Results show
the customer service level, product inventory levels, equipment utilization,
and the daily production schedule. Spreadsheet software supports data entry
and report examination. All software is integrated in a single simulation
environment.
Tuesday 8:30:00 AM 10:00:00 AM
Production Analysis &
Constraints
Chair: Durk-Jouke van der Zee (Universtiy of Groningen)
Applying Discrete Event Simulation and an Automated
Bottleneck Analysis as an Aid to Detect Running Production
Constraints
Patrick Faget and Ulf Eriksson (Volvo Car Corporation)
and Frank Herrmann (Chalmers University of Technology)
Abstract:
Discrete event simulation is an important decision
support tool to evaluate changes in manufacturing, distribution or process
facilities. The challenge arises when it comes to the integration of
simulation as an effective tool to detect manufacturing constraints and to
suggest improvement alternatives. This paper describes the application of a
method for detecting bottlenecks in discrete event models developed by Toyota
Motor Company. The objective in this case is to automate the bottleneck
analysis facilitating the understanding and adoption of simulation by decision
makers without knowledge of simulation. The main results of this paper are the
validation of the bottleneck detection method and its integration with MS
Excel spreadsheets. Moreover system improvement alternatives are presented by
the use of design of experiments.
Simulation Modeling and Analysis of a New Mixed
Model Production Line
Servet Hasgül and Alptuğ Selçuk Büyüksünetçi
(Osmangazi University)
Abstract:
Mixed model production lines are often used in
manufacturing systems. In production lines, different product types are
simultaneously manufactured by processing small batches. This paper describes
a recently completed project involving the development of simulation models
for a mixed model production line in a refrigerator company. Decision maker
wants to determine the bottlenecks before changing the traditional line to a
mixed model production line. Due to the enlarged number of models, the design
of an assembly system becomes more complicated. Performance evaluation is an
important phase in the design of assembly lines in a mixed model production
environment. Simulation models helped us to identify production line
bottlenecks and evaluate some number of suggested solutions.
A Kanban Module for Simulating Pull Production
in ARENA
Mark A. Treadwell and Jeffrey W. Herrmann (University of
Maryland)
Abstract:
In the short timeline of rapid improvement events
(kaizen events), it is difficult to use the full power of simulation because
of the time required to construct models, particularly if the system uses pull
production control methods such as kanbans. This paper describes multiple ways
to model pull production control and compares them on measures related to
model construction and execution. A kanban workstation module significantly
reduces the time required to develop a pull production model, which makes
simulation more useful as a decision-making tool in rapid improvement events.
Tuesday 10:30:00 AM 12:00:00 PM
Production Policy & Cost
Control
Chair: Onur Ülgen (Production Modeling Corporation)
Finding the Optimal Production Control Policy
Using the Production Control Framework
Sean M. Gahagan (Northrop
Grumman Corporation) and Jeffrey W. Herrmann (University of Maryland)
Abstract:
The production control policy affects the performance
of a manufacturing system. Evaluating a production control policy usually
requires simulation modeling due to the complex interactions that occur. This
paper introduces a technique that optimizes production control of single
product flow shops under hybrid production control by using the Production
Control Framework. This simulation modeling template is designed to explore
the production control domain. The paper demonstrates how this template can be
used in conjunction with existing simulation optimization software to find an
optimal production control policy. The decision variables are location of the
push-pull interface and the number of kanbans at each workstation. The
objectives include improving customer service and reducing work-in-process
inventory.
Applying Energy Aspects on Simulation of Energy
Intensive Production Systems
Petter Solding and Damir Petku
(Swedish Foundry Association)
Abstract:
The electricity market within the European Union was
liberalized in 2004, which means that Sweden, together with other countries
with generally low electricity prices, will face higher electricity prices.
This has triggered research with the aim to help energy-intensive companies
reduce their electricity usage and total energy usage as well. This paper
introduces a new concept for simulating energy-intensive production. Using
specially built simulation models helps companies take more than the time
aspect into consideration when planning their production. Often energy and
power utilization is an important aspect to consider when planning, since the
cost for energy and power usage can be high, especially if a “load
subscription” is used and the usage is above the company’s subscribed level.
The methodology described helps breaking down energy parameters into three
groups and gives examples of how the simulation model can be built to take
energy and power into consideration.
Tuesday 1:30:00 PM 3:00:00 PM
Simulation-Data Interface &
Integration
Chair: Jan Oscarsson (University of Skövde)
Lot-sizing Within Capacity-Constrained Manufacturing
Systems Using Time-phased Planning
Silvanus T. Enns and Pattita
Suwanruji (University of Calgary)
Abstract:
Research on lot sizing has mostly assumed single
echelon systems. Even when multiple echelon systems have been used, capacity
constraints are seldom considered. However, in manufacturing capacity
constraints can lead to significant queuing effects. Commonly used lot sizing
policies like Lot-For-Lot (LFL) and Period Order Quantity (POQ) do not take
these effects into account. This research compares these policies with a Fixed
Order Quantity (FOQ) policy, within which lot sizes are based on minimizing
estimated lot flowtimes at capacity-constrained machines. Simulation is used
to study a small production and distribution network using time-phased
planning. Results show that the FOQ policy performs better than both LFL and
POQ when inventory levels and delivery performance are of concern.
Discrete-Event Simulation and Automatic Data
Collection Improve Performance in a Manufacturing System
Arne
Ingemansson and Jan Oscarsson (University of Skövde)
Abstract:
Data utilization from an automatic collection system
helps simulation. DES (Discrete-Event Simulation) is a suitable tool in that
respect. Improvements of a manufacturing system by reducing production
disturbances in block engine line of a truck manufacturer were shown in a case
study. The manufacturing line is equipped with an automatic data gathering
system, collecting detailed information from each machine, such as DT
(DownTime). The collected data and the simulation model were used in finding
bottlenecks in the system. The improvement groups of the company suggested
improvements to these machines in collaboration with DES work. An improvement
of 12% was achieved in the block line during two years. The long-term
improvement work was profitable. Further potential with the method is
investigated in a new case study.
Data Exchange for Machine Shop
Simulation
Y. Tina Lee and Yan Luo (National Institute of Standards
and Technology)
Abstract:
Manufacturing simulation systems normally provide
interfaces for data import and export using proprietary formats. Dependent
data interfaces limit simulation applications in the manufacturing industry.
This paper describes a mechanism for transferring data between a traditional
database and XML files, which represent a machine shop data model developed at
the National Institute of Standards and Technology (NIST). The data model is
described by XML (eXtensible Markup Language) and UML (Unified Model-ing
Language). The data transfer mechanism is based on Document Object Model
(DOM), XML Path Language (XPath), and Open Database Connectivity (ODBC)
database engines. A prototype implementation is also described in this paper.
Tuesday 3:30:00 PM 5:00:00 PM
Simuation and Control
Chair:
Javier Faulin (Public University of Navarra)
Emulation with DSOL
Peter H.M. Jacobs
and Alexander Verbraeck (Delft University of Technology) and William Rengelink
(TBA Nederland)
Abstract:
Manufacturing control systems are extremely hard to
design and test. Testing programmable Logic Controller (PLC) software in an
on-line manufacturing setting can be costly, dangerous, and ineffcient. The
availability of a seamless transition between the real manufacturing process
and a simulated manufacturing process on the one hand, and a real PLC and a
soft PLC on the other hand might help to solve these problems. Using the
Java-based object oriented simulation library DSOL (Distributed Simulation
Object Library), a case study was conducted for a concrete floor manufacturer
to see whether these problems could be overcome. The full simulation and
hardware-in-the-loop tests with DSOL, with the Modbus middleware protocol, and
with real and soft PLCs went fine, and showed the added value of the
distributed, service-oriented paradigm on which DSOL is based.
SAEDES++: Determining Complex System Availability
Via Simulation
Javier Faulin (Public University of Navarra), Angel
A. Juan and Carles Serrat (Technical University of Catalonia) and Vicente
Bargueño (Universidad Nacional de Educación a Distancia)
Abstract:
Complex systems are everywhere among us:
telecommunication networks, computers, transporting vehicles, and electrical
appliances are well known examples. Designing reliable systems and determining
their availability are both very important tasks for managers and engineers,
since reliability and availability have a strong relationship to other
concepts such as quality and safety. Furthermore, these tasks are extremely
difficult, due to the fact that analytical methods can become too complicated,
inefficient or even inappropriate when dealing with sophisticated systems. In
this paper we present the basic ideas behind a simulation-based method, called
SAEDES, which can be very useful when determining availability for a wide
range of complex systems. The method is implemented in C/C++ using two
different algorithms, SAEDES_A1 (component-oriented) and SAEDES_A2
(system-oriented). Two case-studies are introduced and analyzed using both
algorithms, which allows us to compare the associated results.
An SDS Modeling Approach for Simulation-based
Control
Sreeram Ramakrishnan and Mayur Thakur (University of
Missouri-Rolla)
Abstract:
We initiate a study of mathematical models for
specifying discrete simulation-based control systems. It is desirable to
specify simulation-based control systems using a model that is intuitive,
succinct, expressive, and whose state space properties are relatively easy
computationally. We compare automata-based models for specifying control
systems and find that all systems that are currently used (such as finite
state machines, communicating hierarchical finite state machines (FSM),
communicating finite state machines, and Turing machines) lack at least one of
the abovementioned features. We propose using sequential dynamical systems
(SDS)- a formalism for representing discrete simulations to specify
simulation-based control systems. We show how to adapt the standard SDS model
to specify cell-level controllers for a generic cell.
![]()