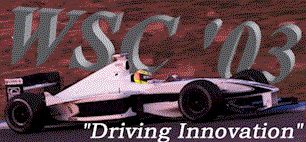 |
WSC 2003 Final Abstracts |
Semiconductor Manufacturing Track
Monday 10:30:00 AM 12:00:00 PM
Factory Scheduling and Dispatching
Chair: Oliver Rose (University of Würzburg)
Constant Time Interval Production Planning with
Application to WIP Control in Semiconductor Fabrication
Kazuo
Miyashita (Natl. Inst. of Advanced Industrial Science & Technology) and
Kazuyuki Senoh, Hiroyuki Ozaki, and Hirofumi Matsuo (Institute of Policy &
Planning Sciences)
Abstract:
We develop a constant time interval production planning
and control methodology, called CONSTIN, and its associated simulation system
for a large-scale and unstable semiconductor manufacturing process. CONSTIN
moves work-in-process inventories (WIP) between processes only at a constant
time interval, and consequently maintains a desirable level of WIP. Our
theoretical and experimental analysis shows a clear relationship between WIP
levels and the time interval in CONSTIN. Computational experiments with
realistic wafer fabrication process data demonstrate that CONSTIN is
comparable in simulation accuracy to a popular event-driven simulator and can
run much faster. Additional experiments also manifest that, with appropriate
control rules, CONSTIN can restore the desired levels of WIP from extreme
deviations and maintain them. Therefore, we conclude that CONSTIN is a
promising methodology of production planning and WIP control for the
semiconductor manufacturing process.
Simulation-Based Assessment of Batching Heuristics
in Semiconductor Manufacturing
Lars Mönch and Ilka Habenicht
(Technical University of Ilmenau)
Abstract:
In this paper, we investigate the performance of
different dispatching and scheduling heuristics for batching tools in a
semiconductor wafer fabrication facility (wafer fab) by means of discrete
event simulation. Because the processing times of lots on batching tools are
quite large compared to those of other processes, careful batching decisions
may have a great impact on the performance of the entire wafer fab. In a first
step, we investigate the performance of certain modifications of the Apparent
Tardiness Cost (ATC) dispatching rule that do not take into account future lot
arrivals. In a second step, we extend this approach by considering future lot
arrivals. In a last step, we combine a genetic algorithm for assignment of the
batches to parallel machines with the ATC rule, which takes future lot
arrivals into account. We present results of simulation experiments with the
different heuristics.
Accelerating Products under Due-Date Oriented
Dispatching Rules in Semiconductor Manufacturing
Oliver Rose
(University of Würzburg)
Abstract:
In semiconductor manufacturing facilities, there is
often the need to speed up certain product types. This is usually done by
either assigning higher priorities or by reducing due dates. In this paper, we
study the effects of accelerating one product type by a tighter due date on
the on-time delivery performance of the other products manufactured. It turns
out that the results depend on the considered factory, its load, and the
accelerated product. As a consequence, it will be hard for production planners
to find simple rules of thumb for the effects of accelerating products. In
general, detailed simulation experiments will be required.
Monday 1:30:00 PM 3:00:00 PM
Automated Material Handling Systems
Chair: David Miller (IBM Microelectronics)
A Simulation-Based Design Framework for Automated
Material Handling Systems in 300mm Fabrication Facilities
Dima
Nazzal and Douglas A. Bodner (Georgia Institute of Technology)
Abstract:
This paper describes a methodology to tackle the
problem of designing Automated Material Handling Systems (AMHS) for 300mm
wafer fabrication facilities. The proposed framework divides the design
process into two levels: architectural and elaborative. Prior to the design,
fab data are preprocessed using simulation of manufacturing operations. The
output data and fab requirements data are then profiled to aid in design
decision making at the architectural level. Once architectural design
decisions are made, lower-level design decisions are made and analyzed using a
simulation model that incorporates the AMHS. Due to the potential number of
alternatives and time constraints on the design process, we are exploring
rapid model generation methods. In this paper, we describe our progress to
date in creating this methodology.
Automated Reticle Handling: A Comparison of
Distributed and Centralized Reticle Storage and Transport
Anne M.
Murray and David J. Miller (IBM Microelectronics)
Abstract:
The implementation of Automated Material Handling
Systems (AMHS) in 300mm semiconductor facilities provides the opportunity to
realize significant benefits in fabricator productivity and performance. The
leverage associated with automated reticle delivery to photolithography
process tools may be less apparent than a fab-wide AMHS. However, a high
product mix environment requires the tracking, storage and transportation of
thousands of reticles to successfully process wafers on photolithography
tools. The failure to deliver reticles in an accurate and timely manner will
negate many of the competitive advantages associated with automated wafer
handling. Implementing an automated reticle management system (ARMS) requires
an evolution from traditional reticle storage and management methodologies. In
this paper, we review the application of simulation analysis to explore
centralized versus distributed reticle storage and handling alternatives for
an overall ARMS strategy.
An Approach to Robust Layout Planning of
AMHS
Roland Sturm, Joachim Seidelmann, Johann Dorner, and Kevin
Reddig (Fraunhofer IPA)
Abstract:
The simulation-based layout planning of automated
material handling systems (AMHS) for microelectronics and semiconductor
manufacturing demands adequate simulation models. An approach for measuring
and quantifying the AMHS layout performance of alternative planning variants
is required. Fraunhofer IPA has developed simulation methods and a three level
approach for calculation of AMHS performance metrics. This approach is very
efficient when comparing alternative planning variants, although the
difference in the configuration change is very small. The paper outlines the
planning approach for two typical AMHS designs used for interbay
transportation in 200mm wafer fabs. The models used are generic and can be
adapted easily to different AMHS solutions.
Monday 3:30:00 PM 5:00:00 PM
Factory Capacity and Throughput
Planning
Chair: Juergen Potoradi (Infineon Technologies)
Conceptualization, Design and Implementation of a
Static Capacity Model
Orkun Ozturk, Melissa Boom Coburn, and Steve
Kitterman (Seagate Technology)
Abstract:
This paper describes the methodology used for
development of a static capacity model. It is a well-known fact that no matter
how sophisticated the dynamic models are, there is always a need for the
simple spreadsheet model. The spreadsheet model helps one carry out simple and
fast analyses whenever they are needed. At the Seagate Technology’s Recording
Head Operations Wafer Manufacturing facility (Bloomington, MN) industrial
engineers who worked on capacity planning devised their own versions of static
spreadsheet models over the years. As useful as these individual models were,
being highly custom-tailored and decentralized made them hard to cross-use and
manage. To overcome this problem, the IE department designed and implemented a
centralized spreadsheet based static capacity model with features that allow
industrial engineers create model outputs the way they want.
Indirect Estimation of Cycle Time Quantiles from
Discrete Event Simulation Models Using the Cornish-Fisher
Expansion
Jennifer E. McNeill, Gerald T. Mackulak, and John W.
Fowler (Arizona State University)
Abstract:
This paper introduces a new technique for estimating
cycle time percentiles from discrete event simulation models run at a single
traffic intensity. The Cornish-Fisher expansion is used as a vehicle for this
approximation, and it is shown that for an M/M/1 system and a full factory
simulation model, the technique provides accurate results with low variability
for the most commonly estimated percentiles without requiring unreasonable
sample sizes. Additionally, the technique provides the advantages of being
easy to implement and providing multiple cycle time percentiles from a single
set of simulation runs.
Discrete-Event Simulation Using SystemC: Interactive
Semiconductor Factory Modeling with FabSim
Holger Vogt (Fraunhofer
IMS)
Abstract:
Semiconductor fabrication factories are large
enterprises with many toolsets, each having multiple production machines. The
process flow is highly reentrant, therefore modeling is best done by
discrete-event simulation. To describe such a fab, the author has developed a
new discrete event simulator called FabSim. It is written in C++. As the
simulation engine it uses SystemC, a C++ class library originally developed
for modeling “Systems on a Chip”. The factory with its machines and lots
traveling and in process is mapped onto SystemC like a hardware description
during RTL (register transfer) modeling. The resulting simulator is compact,
fast and efficient. In a special configuration as a MS Windows dynamic link
library, the simulator is fully interactive. At any time you may define a stop
in the simulation flow, retrieve the state of the whole system, change
parameters, add lots, or even enter a new state and continue with the
simulation.
Tuesday 8:30:00 AM 10:00:00 AM
Process Equipment Modeling
Chair: Robert Wright (SemaTech)
Making Optimal Design Decisions for Next
Generation Dispensing Tools
Brian P. Prescott (Cookson Electronics
Equipment) and Todd LeBaron (Brooks Automation Inc.)
Abstract:
The competitive environment faced by semiconductor
equipment suppliers leaves no room for error when design-ing next generation
tools. In addition, time to market, footprint, and equipment capabilities are
all key to a successful product. At Cookson Electronics Equipment, tool
designers used simulation to answer some difficult design questions, improve
time to market, and lower development costs. This paper explains how
simulation was used in designing the new High Volume Batch (HVB) dispensing
platform. It also discusses the flexible simulation model and simulation
results for various prototype equipment designs.
Application of Cluster Tool Modeling to a 300
mm Fab Simulation
Sameer T. Shikalgar and David Fronckowiak (IBM)
and Edward A. MacNair (IBM T.J. Watson Research Center)
Abstract:
300 mm semiconductor wafer fabrication facilities, like
conventional semiconductor fabs, contain many different types of tools. In
this paper we discuss a realistic way of representing cluster tools in a
simulation model of the entire line. A more realistic representation of
cluster tools results in greater accuracy in the output of the simulation
model.
Resident-Entity based Simulation of Batch Chamber
Tools in 300mm Semiconductor Manufacturing
Nirmal Govind (The
Pennsylvania State University) and David Fronckowiak (IBM Microelectronics)
Abstract:
This paper describes a resident-entity based pilot
simulation study of a class of tools used in 300mm semiconductor manufacturing
known as the wets tools or the wet benches. These are batch chamber tools -
they have several chambers or tanks, each of which can accommodate a batch of
wafers, usually more than one lot size. We develop a simulation model for the
wets processing area that is based on the resident-entity paradigm, but makes
use of transient-entity-type modeling when more information needs to be
tracked. Resident-entity models tend to be much faster than transient-entity
simulation models that are common in semiconductor manufacturing. The model
developed captures most of the internal workings of a wets tool and at the
same time, models different types of tools. We used the model to evaluate the
effects of scheduling policies and batching parameters on the performance of
the wets process area.
![]()