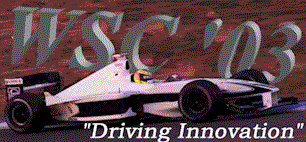 |
WSC 2003 Final Abstracts |
Manufacturing Applications Track
Monday 10:30:00 AM 12:00:00 PM
New Manufacturing Modeling
Methodology
Chair: Silvanus Enns (University of Calgary)
A Hybrid Approach to Manufacturing Enterprise
Simulation
Luis Rabelo and Magdi Helal (University of Central
Florida), Young-Jun Son (University of Arizona), Albert Jones and Jason Min
(National Institute of Standards & Technology) and Abhijit Deshmukh
(University of Massachusetts)
Abstract:
Manufacturing enterprise decisions can be classified
into four groups: business decisions, design decisions, engineering decisions,
and production decisions. Numerous physical and software simulation techniques
have been used to evaluate specific decisions by predicting their impact on
the system as measured by one or more performance measures. In this paper, we
focus on production decisions, where discrete-event simulation models perform
that evaluation. We argue that such an evaluation is limited in time and
scope, and does not capture the potential impact of these decisions on the
whole enterprise. We propose integrating these discrete-event models with
system dynamic models and we show the potential benefits of such an
integration using an example of semiconductor enterprise.
Deterministic and Stochastic Dynamic Modeling of
Continuous Manufacturing Systems Using Analogies to Electrical
Systems
Bashar H. Sader and Carl D. Sorensen (Brigham Young
University)
Abstract:
A dynamic system model of continuous manufacturing
systems has been developed based on analogies with electrical systems. This
model has the capability to model both deterministic and stochastic systems.
The model provides physically meaningful governing equations to describe both
the steady state and transient responses of continuous manufacturing systems.
For stochastic solutions, the model is not limited to any specific
probabilistic distribution. The model is demonstrated by application to a
representative continuous manufacturing line for both deterministic and
stochastic cases. The results of the stochastic case are compared to those
from a discrete event simulation tool using a paired t-test at the 95%
confidence level. For some results, the difference is statistically
insignificant. For others, there is a statistically significant difference.
However, in both cases the percentage difference is within a reasonable range.
Data Driven Design and Simulation System based on
XML
Guixiu Qiao, Frank Riddick, and Charles McLean (National
Institute of Standards & Technology)
Abstract:
Implementing a highly flexible manufacturing approach,
like mass customization manufacturing, demands an integrated design and
simulation system. This system must be able to cope with difficult issues such
as a high level of product variety, uncertainty in the product demand
forecast, and the reconfiguration of manufacturing resources to support the
introduction and integration of new manufacturing capabilities. In this paper,
a data-driven design and simulation system to support flexible manufacturing
is presented. A neutral model of shop information, based on the eXtensible
Markup Language, is used to describe the important information about the
manufacturing facilities and processes, to configure simulation models and to
exchange data between simulation and other manufacturing applications. When
demand changes, the simulation model can be quickly modified to perform
analysis according to the new demand. Manufacturing capabilities and
production processes can be adjusted, layout reconfigured, and resources
reassigned according to the analysis results.
Monday 1:30:00 PM 3:00:00 PM
Distributed Simulation in
Manufacturing
Chair: Farhad Azadivar (University of Massachusetts)
Automobile Manufacturing Supply Chain Simulation in
the GRIDS Environment
Gary Tan and Na Zhao (National University of
Singapore) and Simon J.E. Taylor (Brunel University)
Abstract:
A Supply Chain is the series of activities that an
organization uses to deliver value to its customers. In today's competitive
environment, the globalization of markets has rapidly substituted the
traditional integrated business. The competitive success of an organization no
longer depends only on its own efforts, but relies on the efficiency of the
entire supply chain. Therefore, building an effective supply chain is fast
becoming paramount in today's marketplace. Distributed Supply Chain (DSC)
Simulation has been identified as one of the best means to test and analyze
the performance of supply chains. The Generic Runtime Infrastructure for
Distributed Simulation (GRIDS) is a middleware that supports the reuse and
interoperation of DSC simulations. This paper reports the experience on
employing GRIDS to support the distributed collaboration of an automobile
manufacture supply chain simulation. Several advantages of GRIDS are also
discussed here which make it an ideal middleware for DSC simulations.
EPOCHS: Integrated Commercial Off-the-Shelf
Software for Agent-Based Electric Power and Communication
Simulation
Kenneth M. Hopkinson and Kenneth P. Birman (Cornell
University), Renan Giovanini and Denis V. Coury (University of São Paulo) and
Xiaoru Wang and James S. Thorp (Cornell University)
Abstract:
This paper reports on the development of the Electric
Power and Communication Synchronizing Simulator (EPOCHS), a distributed
simulation environment. Existing electric power simulation tools accurately
model power systems of the past, which were controlled as large regional power
pools without significant communication elements. However, as power systems
increasingly turn to protection and control systems that make use of computer
networks, these simulators are less and less capable of predicting the likely
behavior of the resulting power grids. Similarly, the tools used to evaluate
new communication protocols and systems have been developed without attention
to the roles they might play in power scenarios. EPOCHS utilizes multiple
research and commercial off-the-shelf (COTS) systems to bridge the gap. EPOCHS
is also notable for allowing users to transparently encapsulate complex system
behavior that bridges multiple domains through the use of a simple agent-based
framework.
Simulation of Distributed Manufacturing Enterprises:
A New Approach
Sameh M. Saad, Terrence Perera, and Ruwan
Wickramarachchi (Sheffield Hallam University)
Abstract:
The globalization of markets and world-wide competition
forces manufacturing enterprises to enter into alliances leading to the
creation of distributed manufacturing enterprises. Before forming a
partnership it is essential to evaluate viability of proposed enterprise as
well as how a company’s operations are affected by the proposed virtual
enterprise. Distributed simulation provides an attractive tool to make
decisions on such situations. However, due to its complexity and high cost
distributed simulation failed to gain a wide acceptance from industrial users.
This paper presents a new approach for distributed manufacturing simulation
(DMS) including a formal methodology for DMS and, implementation approach
using current commercial simulation software, employing widely available and
cost effective technologies. The main objective of this work is to promote the
use of distributed simulation particularly in distributed manufacturing by
making it fast to develop and less complicated for implementation.
Monday 3:30:00 PM 5:00:00 PM
Simulation Test Bed for Manufacturing
Analysis
Chair: Robert Lu (Boeing)
A Simulation Test Bed for Production and Supply Chain
Modeling
S. T. Enns and Pattita Suwanruji (University of Calgary)
Abstract:
Production systems and supply chains are difficult to
model at the level of detail required to understand factors affecting the
behavior of material flow. This is particularly true when use of centralized
planning systems, such as MRP or DRP, is of interest. Therefore a test bed,
comprised of a planning module and a simulator module, has been developed.
This test bed is designed to be simple, transparent and flexible. It supports
research as well as training. The planning module uses a spreadsheet-based
interface and logic embedded in extensive VBA macros. The simulator module is
made up of a generic ARENA program that requires no direct modeling inputs
when scenarios are changed. Dynamic communication between the modules is
facilitated using VBA. Transient and steady-state behavior can be observed
under diverse conditions. Production systems or supply chains using MRP/DRP,
re-order points or Kanban systems can be compared.
Benchmarking of a Stochastic Production Planning Model
in a Simulation Testbed
German Riaño (Universidad de los Andes
Bogota), Szu Hui Ng (National University of Singapore), Richard Serfozo and
Steven Hackman (Georgia Institute of Technology) and Lai Peng Chan and Peter
Lendermann (Singapore Institute of Mfg. Technology)
Abstract:
A major problem in production planning is to determine
when to release products into production to meet forecasted requirements.
Recently, Riano et al. (2002) proposed the Stochastic Production Planning
(SPP) model for a multi-period, multi-product system, where the lead time to
produce a product may be random. The model determines release times for the
products that ensure the requirements in each time period are met with desired
probabilities at a minimum cost. This paper describes how an advanced planning
model like SPP can be integrated with discrete event simulation models to make
the simulations more realistic and informative. This paper also compares the
performance of the SPP model with the classical MRP (materials requirements
planning) model, and with a stochastic variation of the MRP model in a
simulation study. The costs associated with the production plans from SPP are
about 10% less than the costs from the other two models.
Comparison of Bottleneck Detection Methods for AGV
Systems
Christoph Roser, Masaru Nakano, and Minoru Tanaka (Toyota
Central Research & Development Labs)
Abstract:
The performance of a manufacturing or logistic system
is determined by its constraints. Therefore, in order to improve the
performance, it is necessary to improve the constraints, also known as the
bottlenecks. Finding the bottlenecks, however, is not easy. This paper
compares the two most common bottleneck detection methods, based on the
utilization and the waiting time, with the shifting bottleneck detection
method developed by us, for AGV systems. We find that the two conventional
methods have many shortcomings compared to the shifting bottleneck detection
method. In the example presented here, conventional methods are either unable
to detect the bottleneck at all or detect the bottleneck incorrectly. The
shifting bottleneck detection method not only finds the bottlenecks but also
determines the magnitude of the primary and secondary bottlenecks.
Tuesday 8:30:00 AM 10:00:00 AM
Simulation in Automotive Industries
Chair: Jason Min (NIST)
Reducing Human Error in Simulation in General
Motors
Demet Wood (General Motors) and Echo A. Harger (Production
Modeling Corporation)
Abstract:
This paper focuses on the steps taken to minimize human
error in simulation modeling in General Motors. While errors are costly and
undesirable in any field, they are especially harmful in simulation which has
been struggling to gain acceptance in the business world for a long time. The
solution discussed in this paper can be summarized as “enter the data once and
use the best tool for the job.”
Paint Line Color Change Reduction in Automobile
Assembly through Simulation
Yong-Hee Han, Chen Zhou, Bert Bras,
Leon McGinnis, Carol Carmichael, and P.J. Newcomb (Georgia Institute of
Technology)
Abstract:
The painting process is an important part of the entire
automobile manufacturing system. Changing color in the painting process is
expensive because of the wasted paint and solvent during color change. By
intelligently selecting cars toward downstream operations at the places where
conveyors converge or diverge, we can reduce the number of such color changes
without additional hardware investment. Discrete Event Simulation is a tool of
choice in analyzing these issues in order to develop an effective and
efficient selection algorithm to ensure the system throughput. The concepts
and methods presented here are also applicable to other discrete event
manufacturing processes where setup reduction is pursued.
Using Empirical Evidence of Variations in Worker
Performance to Extend the Capabilities of Discrete Event Simulations in
Manufacturing
Tim Baines, Linda Hadfield, and Steve Mason
(Cranfield University) and John Ladbrook (Ford Motor Company)
Abstract:
Discrete Event Simulation of manufacturing systems has
become widely accepted as an important tool to aid the design of such systems.
Often, however, it is applied by practitioners in a manner which largely
ignores an important element of industry; namely, the workforce. Workers are
usually represented as simple resources, often with deterministic performance
values. This approach ignores the potentially large effect that human
performance variation can have on a system. A long-term data collection
exercise is described with the aim of quantifying the performance variation of
workers in a typical automotive assembly plant. The data are presented in a
histogram form which is immediately usable in simulations to improve the
accuracy of design assessment. The results show levels of skewness and range
which are far larger than anticipated by current researchers and practitioners
in the field.
Tuesday 10:30:00 AM 12:00:00 PM
Manufacturing Case Studies
Chair: Charles McLean (NIST)
Generic Case Studies for Manufacturing Simulation
Applications
Charles McLean and Guodong Shao (National Institute of
Standards & Technology)
Abstract:
Manufacturing managers typically commission simulation
case studies to support their decision-making processes. These studies are
used to evaluate alternative solutions to manufacturing problems in areas such
as plant layout, scheduling, capacity planning, capital equipment acquisition,
inventory management, and supply chain planning. Procedures for performing
case studies vary from organization to organization, and situation to
situation. It is possible that two different simulation analysts faced with
the same manufacturing problem would perform their case studies differently,
obtain different results, and reach different conclusions. The authors contend
that standardization of the case study methodology and development of generic
case studies would increase the likelihood that the simulation process will be
deterministic, i.e., produce repeatable results. This paper presents
background on case studies and makes recommendations concerning the
advancement of manufacturing simulation case study methods and practices.
Simulation Modeling for Quality and Productivity in
Steel Cord Manufacturing
Can H. Turkseven (Purdue University) and
Gürdal Ertek (Sabanci University)
Abstract:
We describe the application of simulation modeling to
estimate and improve quality and productivity performance of a steel cord
manufacturing system. We describe the typical steel cord manufacturing plant,
emphasize its distinguishing characteristics, identify various production
settings and discuss applicability of simulation as a management decision
support tool. Besides presenting the general structure of the developed
simulation model, we focus on wire fractures, which can be an important source
of system disruption.
NIST XML Simulation Interface Specification at Boeing:
A Case Study
Roberto F. Lu (The Boeing Company) and Guixiu Qiao and
Charles McLean (National Institute of Standards & Technology)
Abstract:
Efficient and consistent simulation data management is
indispensable and a challenging problem to be solved in modeling manufacturing
and business processes. An extensible markup language (XML) based simulation
interface specification is being developed by the National Institute of
Standards and Technology (NIST). The proposed NIST document contains a
prototype generic simulation data specification, which is an endeavor to fill
a void in exchanging reusable simulation data. A case study was performed at
Boeing Commercial Airplanes (BCA), utilizing the NIST XML simulation interface
specification. Entity classes in this case study simulation model contain
asynchronous servers, multi-input-output buffers, bidirectional cranes, labors
(manpower), processes, and machines on different shifts. This model can be
executed from a batch control language document, that is derived from the
proposed NIST XML-based simulation specification. This case study illustrates
a feasible method for using the XML-based NIST specifications in a discrete
event simulation model of a manufacturing process.
Tuesday 1:30:00 PM 3:00:00 PM
Manufacturing Analysis and Control
Chair: Christoph Roser (Toyota)
Buffer Allocation Model based on a Single
Simulation
Christoph Roser, Masaru Nakano, and Minoru Tanaka
(Toyota Central Research & Development Labs)
Abstract:
Allocating buffers in manufacturing systems is one of
easiest ways to improve the throughput of the system, as changes can be
implemented quickly and the initial cost of the change is low. Yet, while an
increase in the buffer size usually increases the throughput, it often also
increases the work in progress and the makespan, therefore increasing the
inventory and the time to the customer. Subsequently, the trade off between
the throughput, the work in progress, and the makespan are of significant
research interest. This paper describes a general prediction model of these
performance measures for different buffer size increases based on only a
single simulation. A fully automated implementation of the simulation analysis
and prediction model for manufacturing systems of any size and complexity is
available. The method can be used for flow shops, job shops, and serial or
parallel systems.
Shared Resource Capacity Analysis in Biotech
Manufacturing
Prasad V. Saraph (Bayer HealthCare)
Abstract:
Simulation is a relatively new tool for business
process analysis in the Biotech industry. This paper discusses an application
of discrete event simulation in analyzing the capacity needs of a shared
resource in the manufacturing facility at Bayer Corporation’s Berkeley site.
The SIGMA® simulation model was used to analyze the workload patterns, run
different workload scenarios, taking into consideration uncertainty and
variability, and provide recommendation on a capacity increase plan. This
analysis also demonstrated benefits of certain operational scheduling
policies. The analysis outcome was used to determine capital investments for
2002. The paper illustrates the power of simulation tools in providing quick
and robust analysis with solutions to planning problems.
Behavior of an Order Release Mechanism in a
Make-to-Order Manufacturing System with Selected Order
Acceptance
Amitava Nandi (Nortel Networks) and Paul Rogers
(University of Calgary)
Abstract:
The value of holding orders in a pre-shop pool, prior
to their release to the factory floor, is a somewhat controversial topic. This
is especially true for make-to-order manufacturing systems, where, if capacity
is fixed and exogenous due dates are inflexible, having orders wait in a
pre-shop pool may cause the overall due date performance of the system to
deteriorate. In such circumstances, selective rejection of orders offers an
alternative approach to dealing with surges in demand whilst maintaining
acceptable due date performance. This paper reports on the behavior of such a
make-to-order manufacturing system under a control policy involving both an
order release component and an order acceptance/rejection component.
Tuesday 3:30:00 PM 5:00:00 PM
Simulation Optimization in Manufacturing
Analysis
Chair: David Clegg (Sheffield Hallam University)
A Simulation-Optimization Approach Using Genetic
Search for Supplier Selection
Hongwei Ding, Lyès Benyoucef, and
Xiaolan Xie (INRIA-Lorraine (The French National Institute for Research in
Computer Science & Control))
Abstract:
The paper presents a simulation-optimization approach
using genetic algorithm to the supplier selection problem. The problem
consists in selecting a portfolio of suppliers from a set of pre-selected
candidates. The supplier selection is a multi-criteria problem which includes
both qualitative and quantitative criteria. In order to select the best
suppliers it is crucial to make a trade off between these tangible and
intangible criteria, some of which may be contradictory. The proposed approach
uses discrete-event simulation for performance evaluation of a supplier
portfolio and a genetic algorithm for optimum portfolio identification based
on performance indices estimated by the simulation. Numerical results on a
real-life case study are presented.
Simulation based Optimization for Supply Chain
Configuration Design
Tu Hoang Truong and Farhad Azadivar
(University of Massachusetts, Dartmouth)
Abstract:
The design of a supply chain network as an integrated
system with several tiers of suppliers is a difficult task. It consists of
making strategic decisions on the facility location, stocking location,
production policy, production capacity, distribution and transportation modes.
This research develops a hybrid optimization approach to address the Supply
Chain Configuration Design problem. The new approach combines simulation,
mixed integer programming and genetic algorithm. The genetic algorithm
provides a mechanism to optimize qualitative and policy variables. The mixed
integer programming model reduces computing efforts by manipulating
quantitative variables. Finally simulation is used to evaluate performances of
each supply chain configuration with non-linear, complex relationships and
under more realistic assumptions. The approach is designed to be robust and
could handle the large scale of the real world problems.
Incorporating Fuzzy Logic Admission Control in
Simulation Models
Qisheng Le (The Louisiana State University) and
Gerald M. Knapp (Louisiana State University)
Abstract:
Admission Control is of great interest in computer,
communication and production network applications. As systems become more
complex or need to make decision based on multiple objectives or require to
satisfy several constraints, Fuzzy Logic Control (FLC) is a natural tool to
handle admission problems. This paper discusses the framework of a tool
developed for easily integrating fuzzy logic admission control into Arena
simulation models. The tool is implemented as a "drop-in" model block that
performs admission control. The block can be configured to perform simple or
priority-based admission, as well as multiple queue selection. The FLC "rules"
are set through a design-time user interface and stored in an MS Access
database. Because multiple FLC blocks may be included in a model, almost any
possible admission scenario (multiple entry points, parallel lines, etc) may
be modeled. A case study is used to demonstrate the developed framework.
Wednesday 8:30:00 AM 10:00:00 AM
Neutral Information Structure for
Manufacturing Simulations
Chair: Luis Rabelo (University of Central
Florida)
Designing Reusable Simulation Modules for Electronics
Manufacturing Systems
Phani S. Mukkamala, Jeffrey S. Smith, and
Jorge F. Valenzuela (Auburn University)
Abstract:
Developing simulation models for related problems in
the same domain is generally a repetitive process. Such simulation models are
similar in many aspects and have only minor differences. Modeling efforts can
be reduced to a great extent through the development of domain specific
modules or templates that encapsulate the domain-specific logic and hide many
of the modeling details. This paper describes the development of such a
domain-specific template for electronics assembly. In particular, the template
focuses on the automated assembly of printed circuit boards. The template
encompasses the complexity of the target domain and simplifies the
model-building process. While the paper focuses on a language-neutral
description of the template, specific experience with Arena is described.
Information Structure to Support Discrete Event
Simulation in Manufacturing Systems
Björn Johansson, Joacim
Johnsson, and Anders Kinnander (Chalmers University of Technology)
Abstract:
Discrete Event Simulation (DES) is ranked among the top
three tools for management support. However, it lags in becoming the
successful tool in the industry that many experts have predicted. In this
paper, sixteen projects accomplished in the area of DES have been analyzed in
order to find the reasons for this delay. Most important is the lack of
reliable manufacturing data in companies. This is due to inadequate practices
within the organization, thus forcing users to build simulation models with
estimated data. The paper also answers other questions as to why DES is an
underutilized decision tool. DES is an information-intensive tool for
decision-making, but has weak support concerning working procedures within
organizations. Continuous generation of manufacturing data at all levels has
to be supported by the working procedure in order to increase the use of DES
as an everyday tool. How to improve this situation also is discussed.
A Neutral Information Model for Simulating Machine
Shop Operations
Y. Tina Lee (National Institute of Standards &
Technology), Charles McLean (National Institute of Standards & Technology
(NIST)) and Guodong Shao (National Institute of Standards & Technology)
Abstract:
Small machine shops typically do not have the resources
to develop custom simulations of their operations or data translators to
import their data from other manufacturing software applications. This paper
presents an overview of an information model currently under development at
the National Institute of Standards and Technology (NIST) to address this
problem. The model provides neutral data interfaces for integrating machine
shop software applications with simulation. The information model provides
mechanisms for describing data about organizations, calendars, work,
resources, schedules, parts, process plans, and layouts within a machine shop
environment. The model has been developed using the Unified Modeling Language
(UML) and the Extensible Markup Language (XML).
Wednesday 10:30:00 AM 12:00:00 PM
Supply Chain Simulation
Chair: Steve Buckley (IBM TJ Watson Research
Center)
Distributed Supply Chain Simulation Using a Generic
Job Running Framework
Haifeng Xi, Heng Cao, Leonard Berman, and
David Jensen (IBM T.J. Watson Research Center)
Abstract:
For supply chain performance simulation that involves
aggregating results from multiple runs of the same underlying model,
simulation iterations can be distributed to networked computing resources to
achieve significant speedup. This paper presents a generic distributed job
running framework that facilitates such high performance supply chain
simulation. We first introduce a supply chain modeling and simulation tool
developed by IBM Research, and summarize the strategy to enhance it. A closer
look is then taken at a generic job running framework we designed and how it
was used to bring the distributed simulation capability to the tool. After
reviewing an ongoing effort to integrate the new tool with the IBM MathGrid
environment, we conclude the paper with a brief discussion of our future work.
A Simulation-Based Tool for Inventory Analysis in a
Server Computer Manufacturing Environment
Heng Cao, Feng Cheng,
Haifeng Xi, Markus Ettl, and Stephen Buckley (IBM T.J. Watson Research) and
Carlos Rodriguez (IBM Enterprise Server Group)
Abstract:
In this paper, we describe a simulation-based inventory
management tool developed for the IBM Enterprise Server Group. Through the Web
interface of the tool, an inventory manager is able to visualize Days of
Supply (DOS) levels – current and projected, and to carry out what-if scenario
analysis to identify potential opportunities for improvement. The highly
complicated server manufacturing environment poses simulation modeling
challenges such as two-stage fabrication/fulfillment process, multi-echelon
bills-of-materials, complex server box configurations, part tests with random
yields, stochastic lead times and so on. In the following sections, we will
introduce the common characteristics of the server manufacturing environment,
present the overall architecture of our tool, and describe the simulation
model design and how we addressed those challenges. At the end of the paper,
we will show some results collected from the tool and point out our future
research directions.
A Bayesian Framework for Modeling Demand in Supply
Chain Simulation Experiments
David F. Muñoz (Instituto Tecnológico
Autónomo de México)
Abstract:
In order to postpone production planning based on
information obtained close to the time of sale, decision support systems for
supply chain management often include demand forecasts based on little
historical data and/or subjective information. Particularly, when simulation
models for analyzing decisions related to safety inventories, lot sizing or
lead times are used, it is convenient to model (daily) demand by considering
historical data, as well as information (often subjective) of the near future.
This article presents an approach for modeling a random input (e.g., demand)
in simulation experiments. Under this approach, the family of distributions
proposed for modeling demand should include two types of parameters: the ones
that capture information of historical data and the ones that depend on the
particular scenario that is to be simulated. The approach is extended to the
case where uncertainty on the appropriate family of distributions is present.
![]()