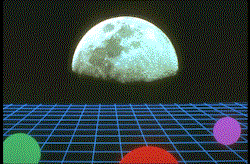 |
WSC 2002 Final Abstracts |
Semiconductor Manufacturing Track
Monday 10:30:00 AM 12:00:00 PM
Wafer Fabrication
Chair: Chad
DeJong (Intel Corporation)
Effects of Metrology Load Port Buffering in Automated
300mm Factories
Robert Wright, Marlin Shopbell, Kristin Rust, and
Silpa Sigireddy (International SEMATECH)
Abstract:
This paper describes a simulation study characterizing
the advantages and disadvantages of implementing multiple load ports on
metrology equipment in a semiconductor factory. Three methods of automated
material handling (AMH) for 300 mm wafer carriers in four separate models were
analyzed: Through Stocker, Point-to-Point, and Conveyor (slow and fast
velocity). Parameters measured include idle times of metrology equipment as
number of load ports change and the effects on bottleneck equipment, work in
process (WIP), queue lengths, transport times, delays waiting for
transportation to begin, and the effect on stocker utilization by bay.
300mm Wafer Fabrication Line Simulation
Model
Sameer T. Shikalgar, David Fronckowiak, and Edward A. MacNair
(IBM)
Abstract:
The importance of semiconductor wafer fabrication has
been increasing steadily over the past decade. Wafer fabrication is the most
technologically complex and capital intensive phase in semiconductor
manufacturing. It involves the processing of wafers of silicon in order to
build up layers and patterns of metal and wafer material. Many operations have
to be performed in a clean room environment to prevent particulate
contamination of wafers. Also, since the machines on which the wafers are
processed are expensive, service contention is an important concern. All these
factors underline the importance of seeking policies to design and operate
them efficiently. We describe a simulation model of a planned 300mm wafer
fabrication line that we are using to make strategic decisions related to the
factory.
Realizing 300mm Fab Productivity Improvements through
Integrated Metrology
K. J. Stanley and Timothy D. Stanley
(International SEMATECH) and Jose' Maia (Technical University of Lisbon)
Abstract:
The operational cost of 300mm wafer production is
significantly greater than that of 200mm fabs. Real-time monitoring of product
can save time and money through reduced scrap and decreased cycle time.
Current process monitoring generally incorporates stand-alone metrology, which
is time consuming and requires excessive wafer handling by production
operators. The benefits of integrated metrology are measured by considering
the impact of metrology on a semi-conductor fab through simulation modeling.
Since the process and metrology steps are in series, overall process
throughput depends on metrology methods. Furthermore, the measurements impact
WIP (Work In Process) inventory. WIP is at risk if the process drifts.
Send-ahead samples reduce WIP risk but also reduce process throughput and tool
utilization. Integrated metrology minimizes risk but may decrease throughput
rate. This paper explores the operational benefits of integrated metrology
strategies versus stand-alone metrology via simulation modeling.
Monday 1:30:00 PM 3:00:00 PM
Material Handling
Chair: Oliver
Rose (University de Wuerzburg)
Operational Modeling and Simulation of an Inter-Bay
AMHS in Semiconductor Wafer Fabrication
Jesus Jimenez, Bosun Kim,
John Fowler, Gerald Mackulak, and You In Choung (Arizona State University) and
Dong-Jin Kim (Samsung Electronics)
Abstract:
This paper studies the operational logic in an
inter-bay automated material handling system (AMHS) in semiconductor wafer
fabrication. This system consists of stockers located in a two-floor layout.
Automated moving devices transfer lots between stockers within the same floor
(intra-floor lot transfer) or between different floors (inter-floor lot
transfer). Intra-floor lot-transferring transports use a two-rail
one-directional system, whereas inter-floor lot-transferring transports use
lifters. The decision problem consists of selecting rails and lifters that
minimize average lot-delivery time. Several operation rules to deliver lots
from source stocker to destination stocker are proposed and their performance
is evaluated by discrete event simulation.
Data-Based Node Penalties in a Path-Finding
Algorithm in an Automated Material Handling System
Miki Fukunari,
Srinivas Rajanna , Robert J. Gaskins, and Mary Ellen Sparrow (Brooks-PRI
Automation, Inc.)
Abstract:
Increasing factory throughput is a critical issue in
the semiconductor industry, and a quick transition of material to the next
location in the automation system plays a significant role in increasing
throughput. A dynamic path-finding algorithm for a vehicle-based automated
material handling system (AMHS) is discussed in this paper. The dynamic
path-finding algorithm uses distance between nodes, node penalties, and the
number of vehicles queued to calculate the total cost of a path. This paper
introduces the use of historical data from the AMHS and discusses how to
effectively utilize such data in critical situations to improve overall AMHS
performance.
Simulating the Transport and Scheduling of Priority
Lots in Semiconductor Factories
Chad D. DeJong and Scott P. Wu
(Intel Corp.)
Abstract:
As the high technology product market becomes more
dynamic and competitive, chip manufacturers need to bring products to
customers in short periods of time. As a result, semiconductor fabrication
plants regularly contain lots with priority status. These lots have several
unique characteristics compared to other production lots, both in terms of lot
transport and scheduling on tools. These lots consume tool capacity that may
impact the factory output rate. Priority lots also have specific policies for
transport. The impact of these priority lots on other lots in the fab is not
easily quantified, as many factors are involved. Dynamic factory and AMHS
simulation models are capable of capturing the variability of a factory, and
the interactions of critical constraints that prevent predictable
manufacturing. This paper presents a breakthrough modeling approach to study
the behaviors of priority lots, and to quantify their impact to manufacturing.
Monday 3:30:00 PM 5:00:00 PM
Scheduling and Dispatching
Chair:
Russell Barton (The Pennsylvania State University)
A Simulation Study on Release, Synchronization, and
Dispatching in MEMS Fabrication
Lixin Wang (Gintic Institute of
Manufacturing Technology) and Loo Hay Lee (National University of Singapore)
Abstract:
MEMS (microelectromechanical system) fabrication can be
organized as three sub-processes, that is, the front-end process, the wafer
cap process, and the back-end process. The coordination between the releases
of raw wafers to the two parallel sub-processes, the front-end process, and
the wafer cap process, is always an important issue. Previous research work
has developed synchronization rules to create effective coordination. In this
paper, new synchronization rules and dispatching rules are developed and they
are evaluated with more release rules. From this much more extensive
simulation experiment, it is found that there are significant two-factor and
three-factor interactions among these three types of rules and we have to
consider them all together in order to achieve the best performance for MEMS
fabrication system. Moreover, the complicated relationship between the
performances (cycle time and total work-in-process) is also indicated.
Some Issues of the Critical Ratio Dispatch Rule in
Semiconductor Manufacturing
Oliver Rose (University of Würzburg)
Abstract:
In this paper, we examine the cycle time and on-time
delivery performance of a semiconductor wafer fabrication facility (wafer fab)
under critical ratio (CR) dispatch regime. It turns out that determining
appropriate due dates for this rule is a critical task. We provide a detailed
analysis of the wafer fab behavior for a large range of due date values. From
the results of the experiments we develop a heuristic for conservative due
date estimates.
A Finite-Capacity Beam-Search-Algorithm for Production
Scheduling in Semiconductor Manufacturing
Ilka Habenicht (Technical
University of Ilmenau) and Lars Mönch (Tecnical University of Ilmenau)
Abstract:
In this paper we describe a finite-capacity algorithm
that can be used for production scheduling in a semiconductor wafer
fabrication facility (wafer fab). The algorithm is a beam-search-type
algorithm. We describe the basic features of the algorithm. The implementation
of the algorithm is based on the ILOG-Solver libraries. We describe the
simulation environment, which is used to evaluate the performance of the
proposed algorithm. We show some results from computational experiments with
the algorithm and the simulation test-bed described.
Tuesday 8:30:00 AM 10:00:00 AM
Modeling Methodology
Chair:
Dave Miller (IBM)
New Approaches for Simulation of Wafer
Fabrication: The Use of Control Variates and Calibration
Metrics
Chanettre Rasmidatta, Shari Murray, John W. Fowler, and
Gerald T. Mackulak (Arizona State University)
Abstract:
Simulation-based wafer fabrication optimization models
require extensive computational time to obtain accurate estimates of output
parameters. This research seeks to develop goal-driven optimization
methodologies for a variety of semiconductor manufacturing problems using
appropriate combinations of "resource-driven" (R-D), "job-driven" (J-D), and
Mixed (combination of R-D and J-D) models to reduce simulation run times. The
initial phase of this research investigates two issues: a) the use of the R-D
simu-lation control variates for the J-D simulation and b) development of
metrics that calibrate the output from the R-D and J-D modeling paradigms. The
use of the R-D model as a control variate is proposed to reduce the variance
of J-D model output. Second, in order to use the R-D model output to predict
the J-D model output, calibration metrics for the R-D and J-D modeling
approaches were developed. Initial developments were tested using an M/M/1
queuing system and an M/D/1 queuing system.
Simulation based Cause and Effect Analysis of Cycle Time
and WIP in Semiconductor Wafer Fabrication
Chao Qi, Tuck Keat Tang,
and Appa Iyer Sivakumar (Nanyang Technological University)
Abstract:
Semiconductor wafer fabrication is perhaps one of the
most complex manufacturing processes found today. In this paper, we construct
a simulation model of part of a wafer fab using ProModel® software and analyze
the effect of different input variables on selected parameters, such as cycle
time, WIP level and equipment utilization rates. These input variables include
arrival distribution, batch size, downtime pattern and lot release control.
SEMATECH DATASET which has the original actual wafer fab data is used for our
analysis.
Using Simulation to Understand Capacity Constraints
and Improve Efficiency on Process Tools
Manuel Aybar and Kishore
Potti (Texas Instruments) and Todd LeBaron (Brooks-PRI Automation)
Abstract:
Finding hidden capacity and maximizing cluster tool
throughput is a common goal for today’s semiconductor manufacturers. This
presentation will discuss a flexible and accurate simulation program capable
of modeling a wide range of semiconductor process tools. The simulation
program provides visibility and understanding into the internal dependencies
and interactions of each process tool. This information provides a solid base
from which sound decisions can be made. Simulation results from two case
studies will be presented. The real-world capacity improvements, cycle time
reductions, and cost savings will be presented.
![]()